ÉTUDE DE CAS DE SAFRAN LANDING SYSTEM
Safran Landing System (anciennement appelé Messier-Bugatti-Dowty) est le leader mondial dans la conception, le développement, la fabrication et la prise en charge des circuits de train d’atterrissage.
Une combinaison unique de capacités d’ingénierie avancées, de la technologie des systèmes intégrés et de l’expérience sur une gamme exclusive de programmes permet à Safran Landing Systems de fournir des solutions innovantes pour une gamme variée d’aéronefs.
Nikken a reçu de la société une proposition de collaboration en 2007 sur un projet d'optimisation d'une application d'usinage de semi-finition de poutres de bogie d'Airbus A350. La solution finale a nécessité l'usinage simultané de 6 pièces forgées en titane de 583 kg sur une plateforme de machine-outil verticale à six broches Droop & Rein.
L’application originale a usiné 3 poutres de bogie sur une machine à indexation manuelle. Chaque opération d'indexation, sur cette base manuelle, prenait 15 minutes à réaliser et nécessitait un opérateur pour effectuer la procédure à l'intérieur de la machine-outil - pas vraiment idéal dans un environnement contaminé par des copeaux de titane et du liquide de refroidissement.
L’intégration sur le socle de la machine de six composants pris en charge par les tables rotatives à commande numérique par ordinateur a nécessité un certain degré d’ingéniosité dans l’ingénierie. Avec 3500 mm entre les centres des composants, la solution an nécessité les tables d’appui TAT320 de Nikken pour être montée dos à dos au centre du socle de la machine. Cela a optimisé l’espace et a permis de maintenir à un minimum absolu la distance entre les composants. Sur le côté de la table rotative, six tables rotatives Nikken CNC601B ont été montées à chaque extrémité du banc, ce qui a permis d'obtenir un maximum d'espace disponible pour l'usinage. En réalisant cette disposition, un espace supplémentaire est également disponible sur le banc de la machine pour accueillir des composants plus grands si les exigences de l'avion changent, ce qui augmente la taille de spécification du composant à l'avenir.
Avec les tables rotatives à commande numérique par ordinateur installées et intégrées, chaque opération d'indexation dure 15 secondes et supprime la nécessité pour l'opérateur d'entrer dans la zone de la machine, ce qui apporte une amélioration significative des pratiques de travail. Le résultat final est une amélioration significative du temps d'exécution pour une charge de six composants, y compris avec dix changements d'outils, ce qui représente un gain d'heures impressionnant. Au regard de la valeur de chaque charge de six composants, il est essentiel pour Safran de s’assurer de l’optimisation du processus afin de garantir 100 % de précision tout en réduisant les temps de cycle.
L'intégration de la commande CNC a été réalisée par Siemens, en utilisant une commande Siemens 840D pour entraîner la machine-outil à six broches ainsi que les six tables rotatives CNC et les unités TAT.
Cette application est une vitrine pour Safran, les gains d'efficacité obtenus en passant à une solution CNC complète indiquent la voie à suivre dans la production de grands composants aéronautiques, avec un accent continu sur l'amélioration des processus pour minimiser l'intervention humaine et réduire le temps nécessaire à la fabrication de chaque composant.
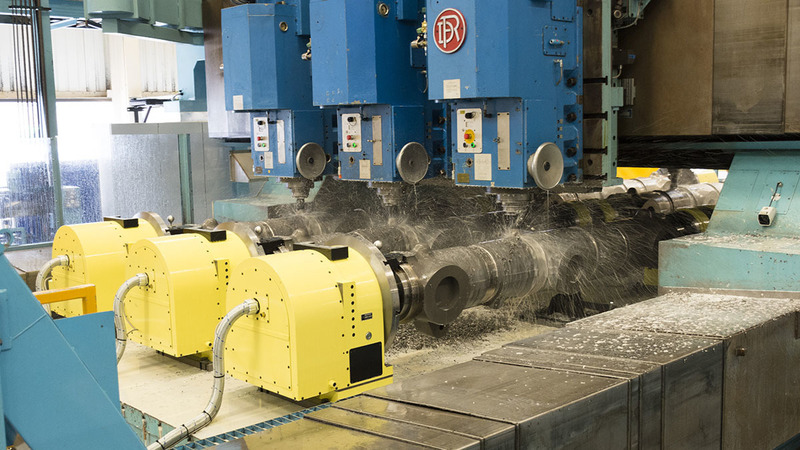
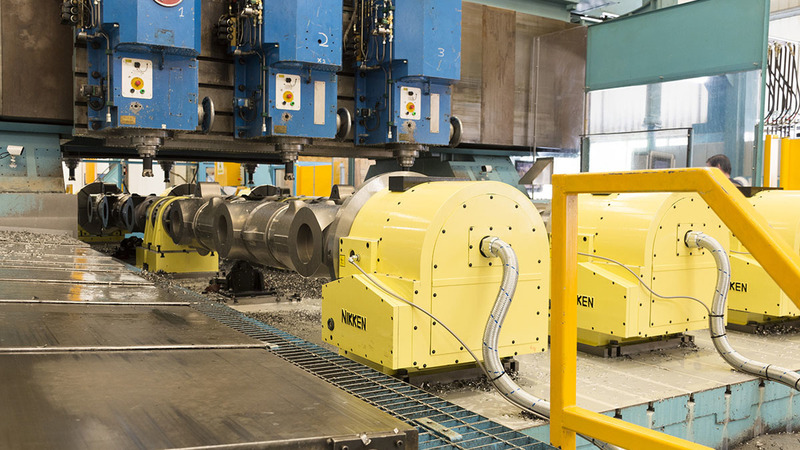
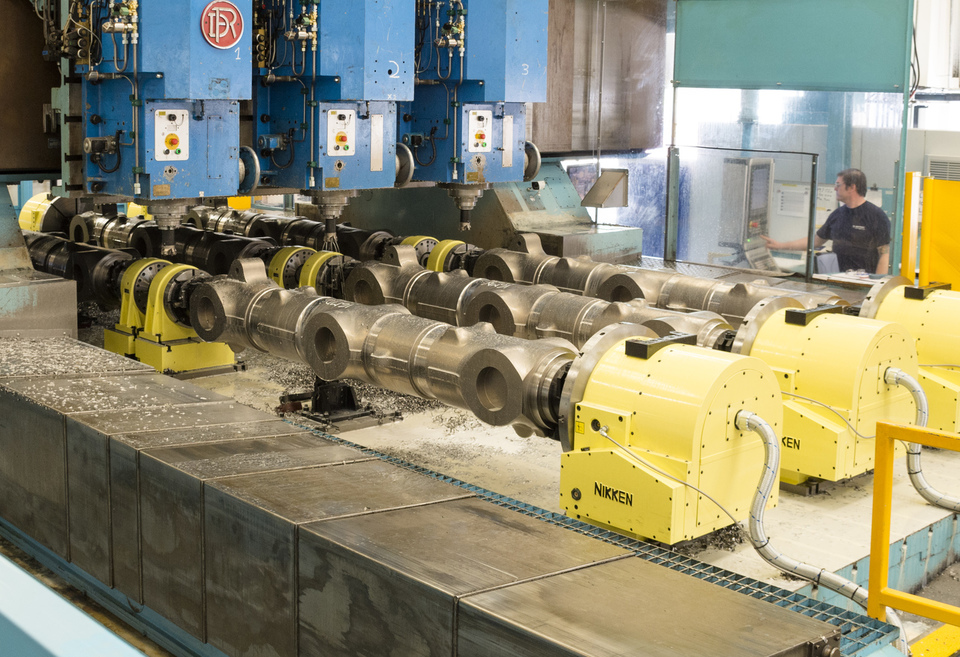